STEAM-HYDROGEN TURBOJET SYSTEM
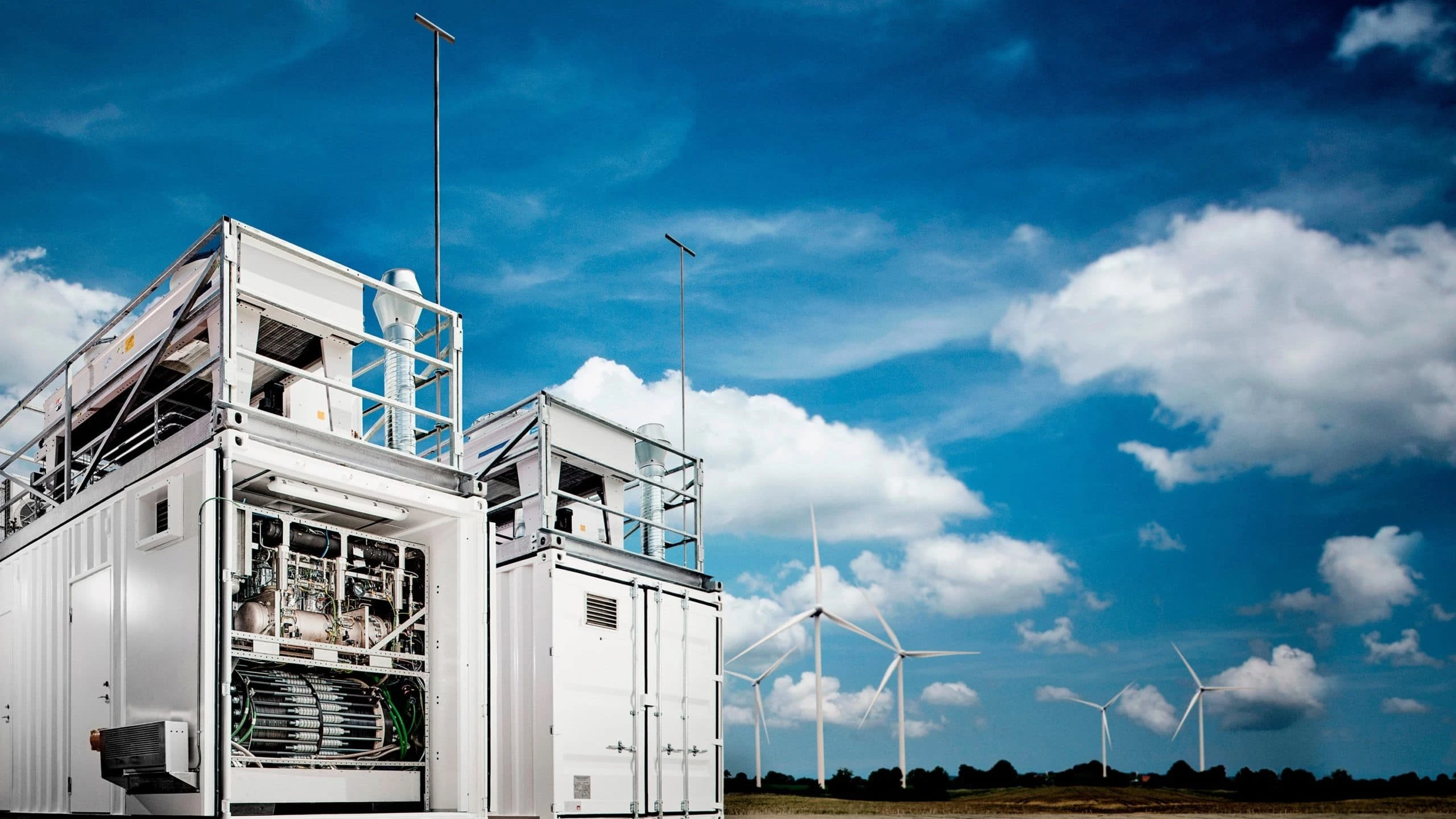
STEAM-HYDROGEN TURBOJET SYSTEM FOR GENERATING ELECTRICITY AND HEAT
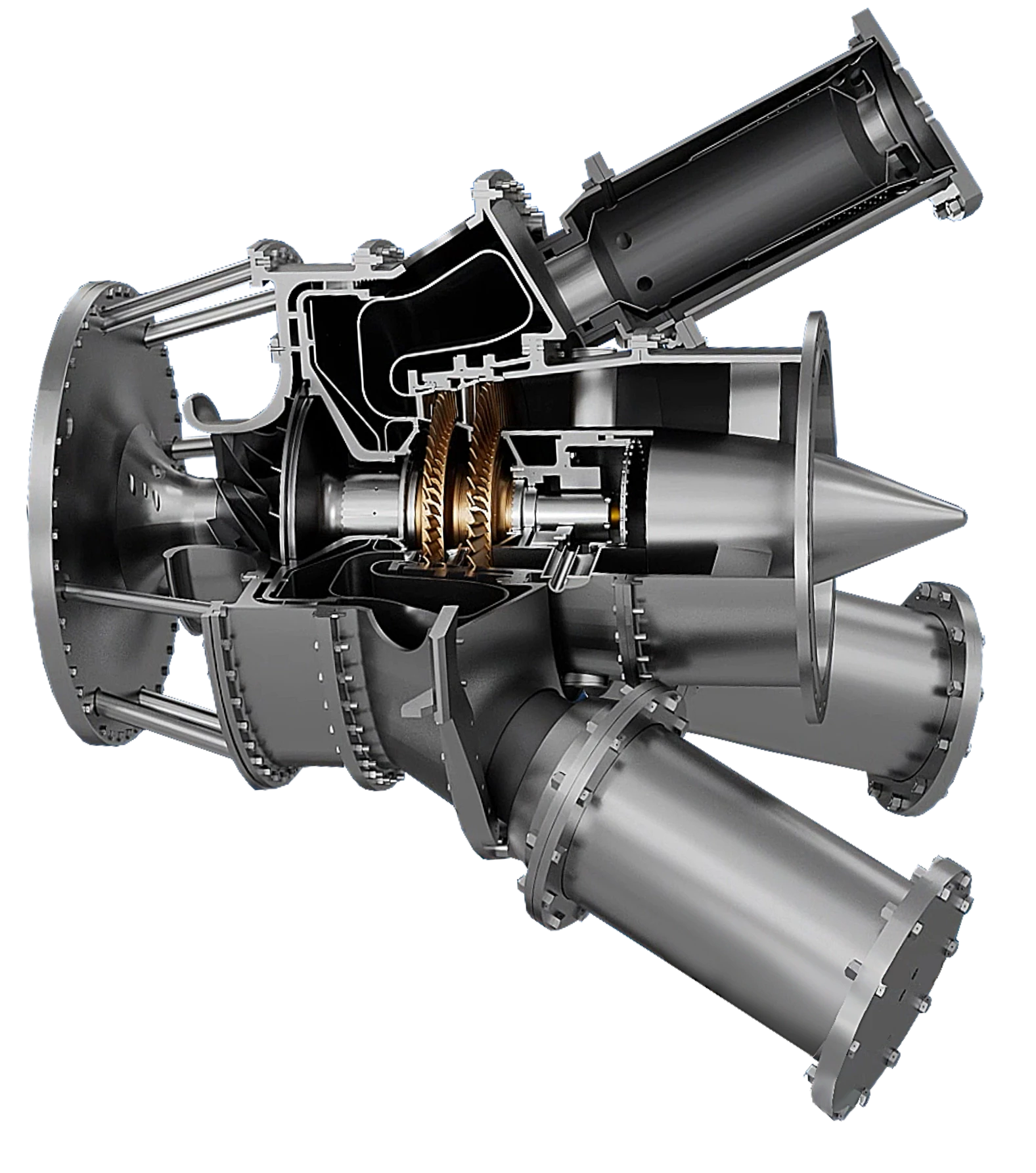
Innovative steam-hydrogen turbojet system for generating electricity and heat is a conceptually new technology based on the principle of catalytic reforming with a preliminary cavitation process of any types of fuel into a high-energy gas fluid (synthesis gas). During the cavitation process, hydrocarbon fuels are dispersed with deionized water under specific pressure and temperature, leading to gasification.
The resulting gas fluid has energy properties several times higher than any conventional fuel. A high-speed next-generation generator with permanent magnets and direct drive on levitating magnetic bearings, "MAGLEV" further reduces energy consumption, noise, and increases the efficiency of the entire system. The turbojet system has no bearing friction, requires no lubrication, and is maintenance-free. It is fully automatic and energy-independent.
By utilizing the formation of high-energy steam-hydrogen fluid, it is the most energy-efficient and environmentally friendly turbojet power plant in the world.
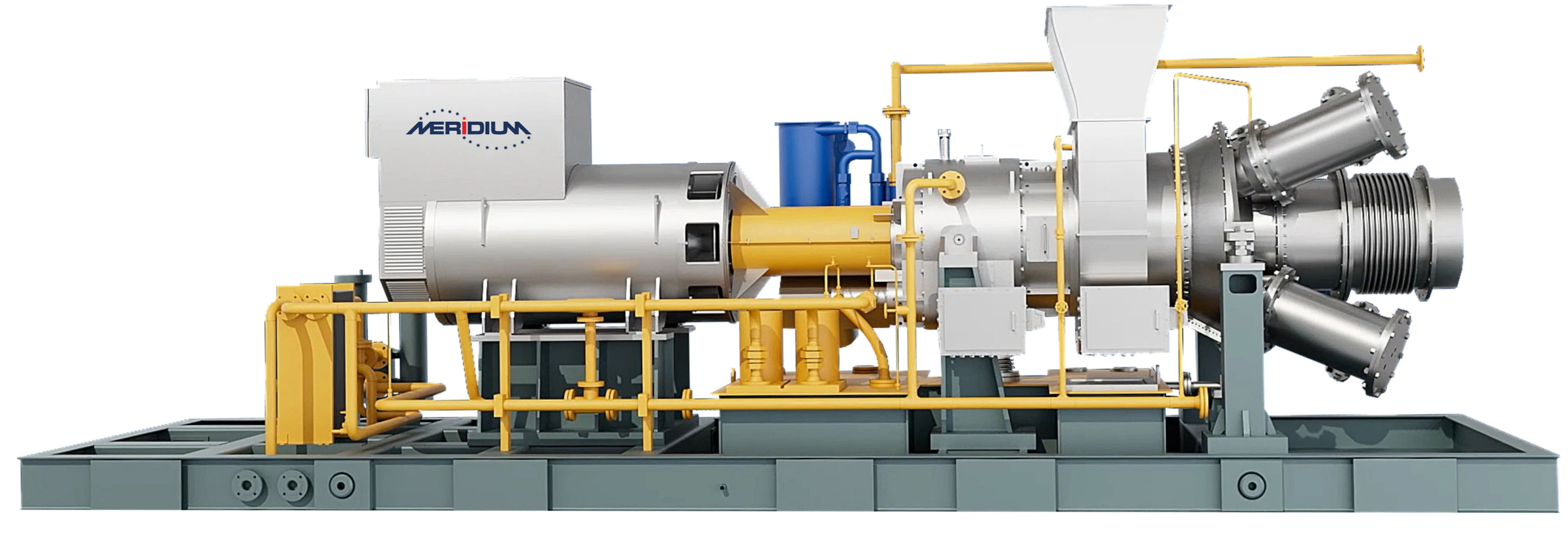
A STEAM-GAS TURBINE FOR GENERATING ELECTRICITY USING AN INNOVATIVE METHOD WITH REACTIVE STEAM-HYDROGEN THRUST.
This method is based on the supercritical state of water steam. In this method, a closed cycle of cold and hot circuits with intermediate steam condensation for reuse is used. high efficiency, cost-effectiveness, and environmental cleanliness are guaranteed.
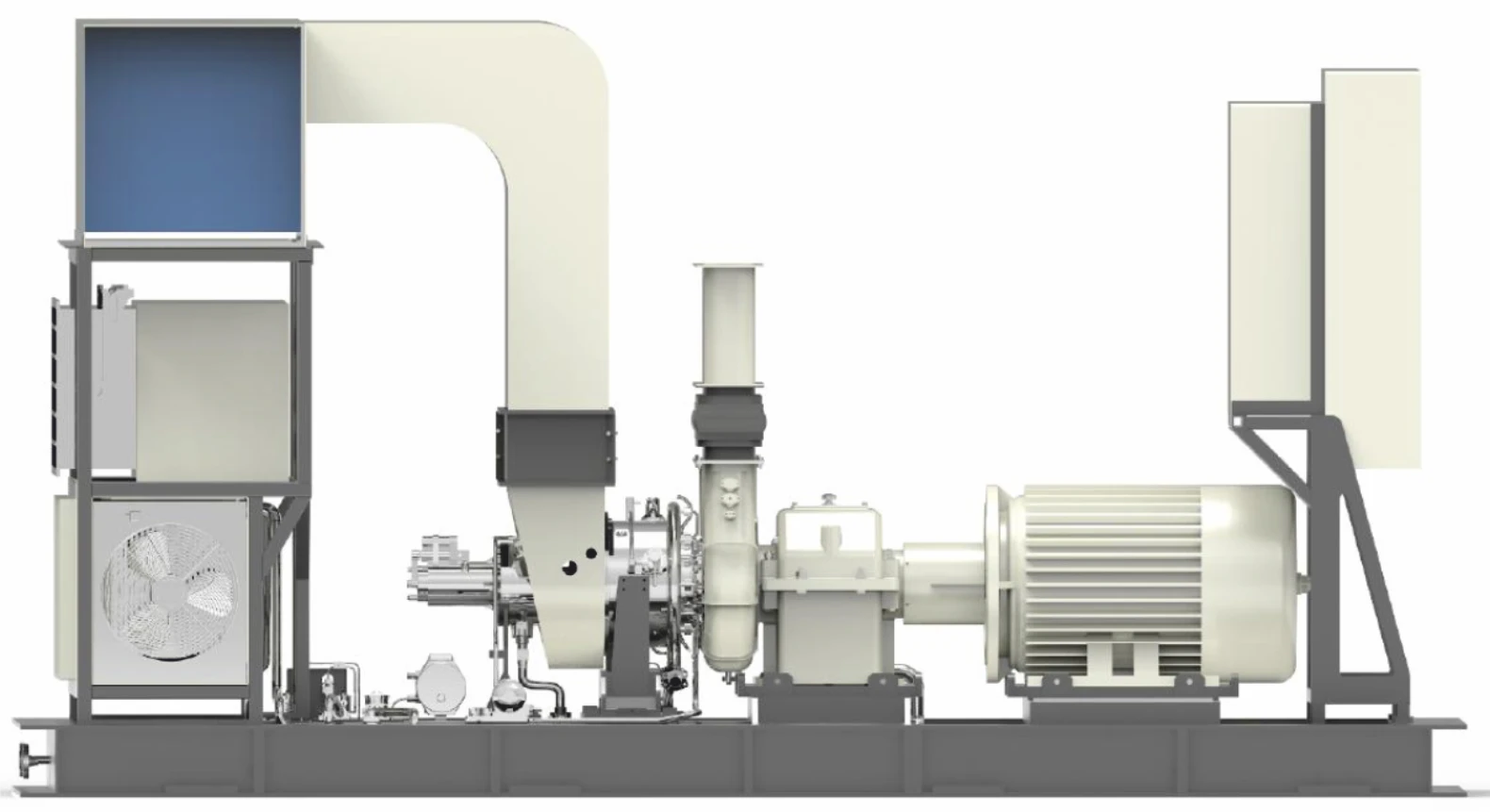
A COMPACT, FULLY AUTONOMOUS, MULTI-FUEL HYBRID POWER PLANT WITH A STEAM-HYDROGEN CATALYTIC JET ACCELERATOR AND AN ENERGY STORAGE BATTERY PACK.
Available in diesel generator and gas piston generator versions with a power output ranging from 50 to 2500 kw.
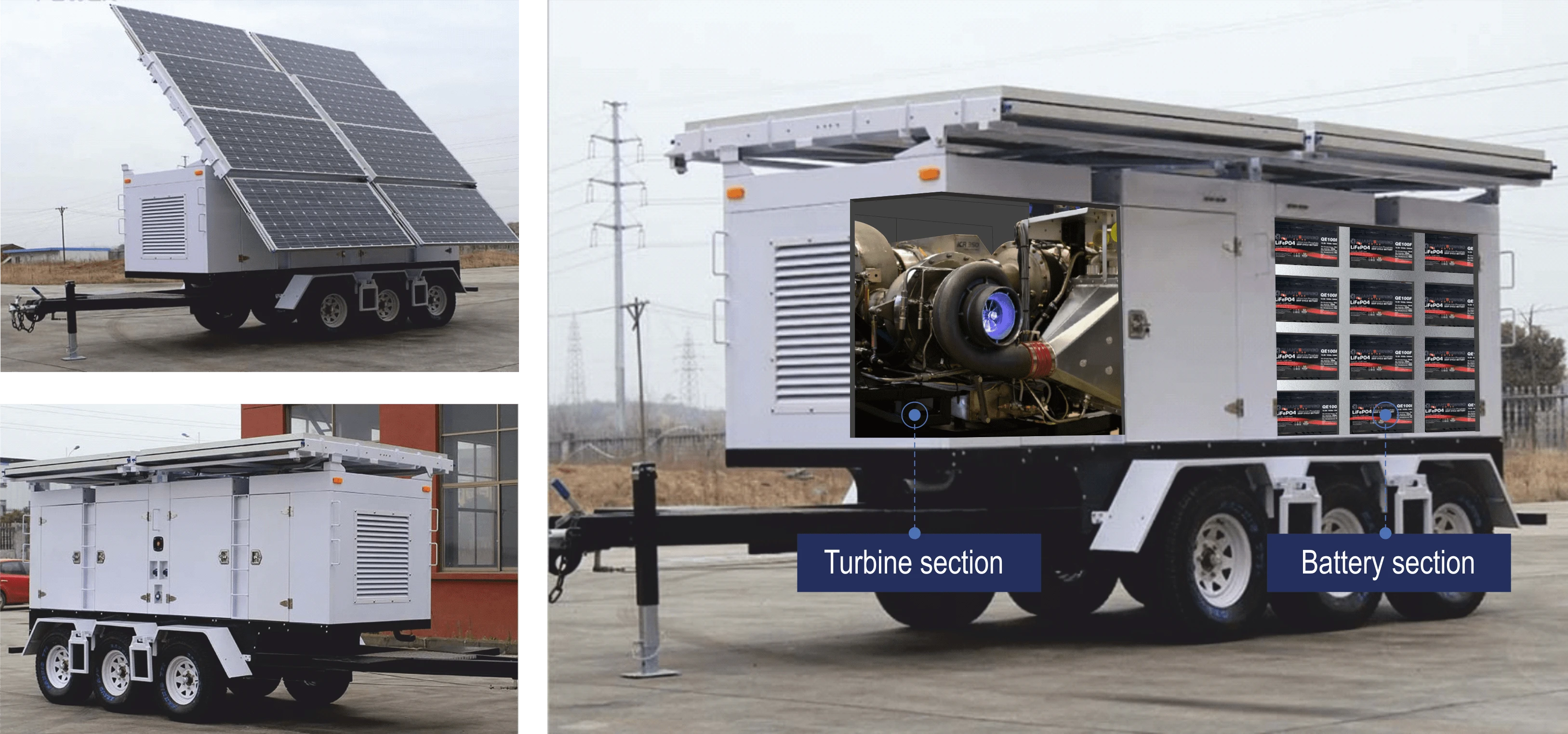
A LONG-TERM ENERGY STORAGE SYSTEM BASED IN A 20/40-FOOT CONTAINER.
Equipped with LiFePO4 batteries with a full charge discharge of up to 9000 cycles (up to 15 years).
Stored power capacity - up to 5 mwh.
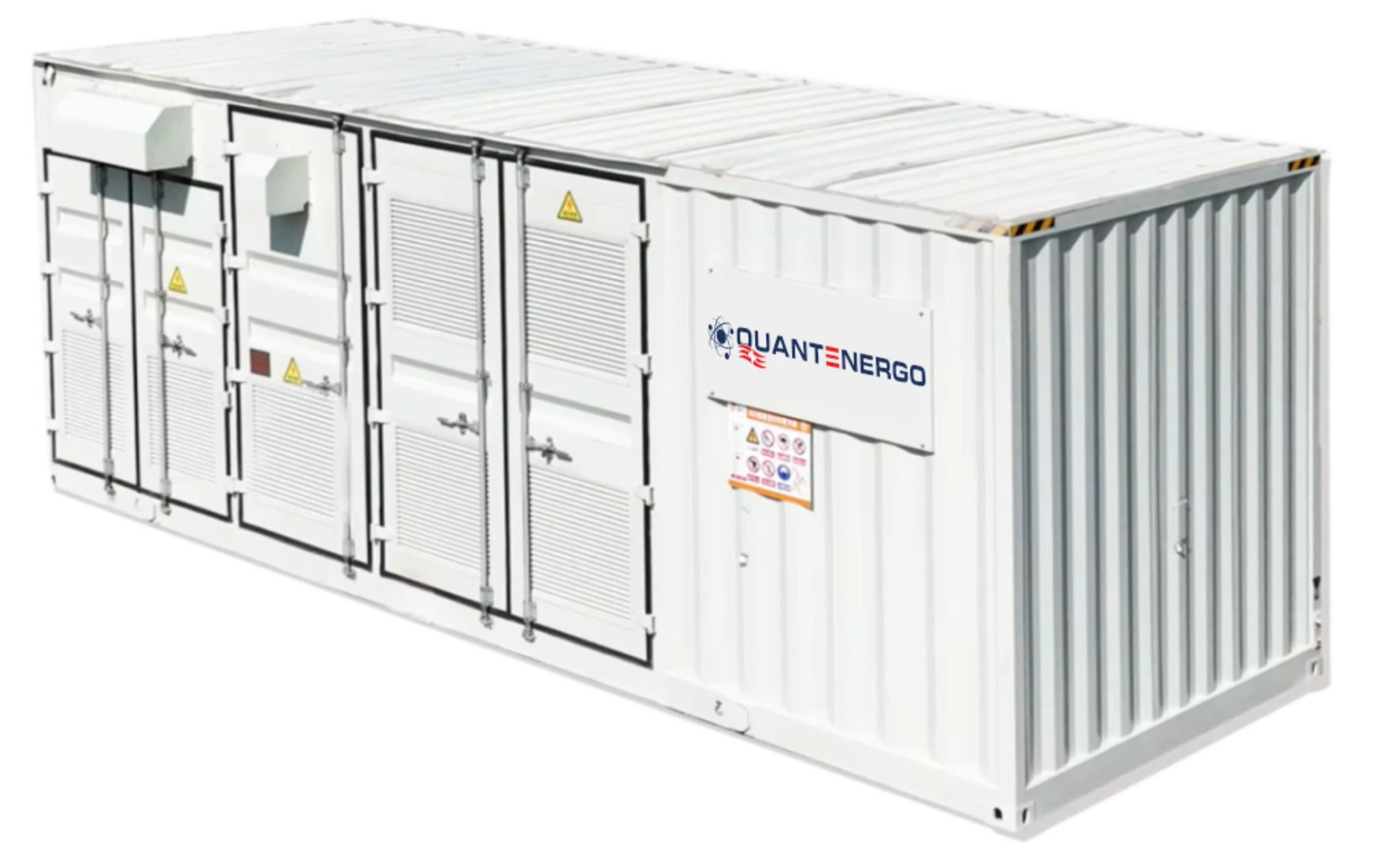
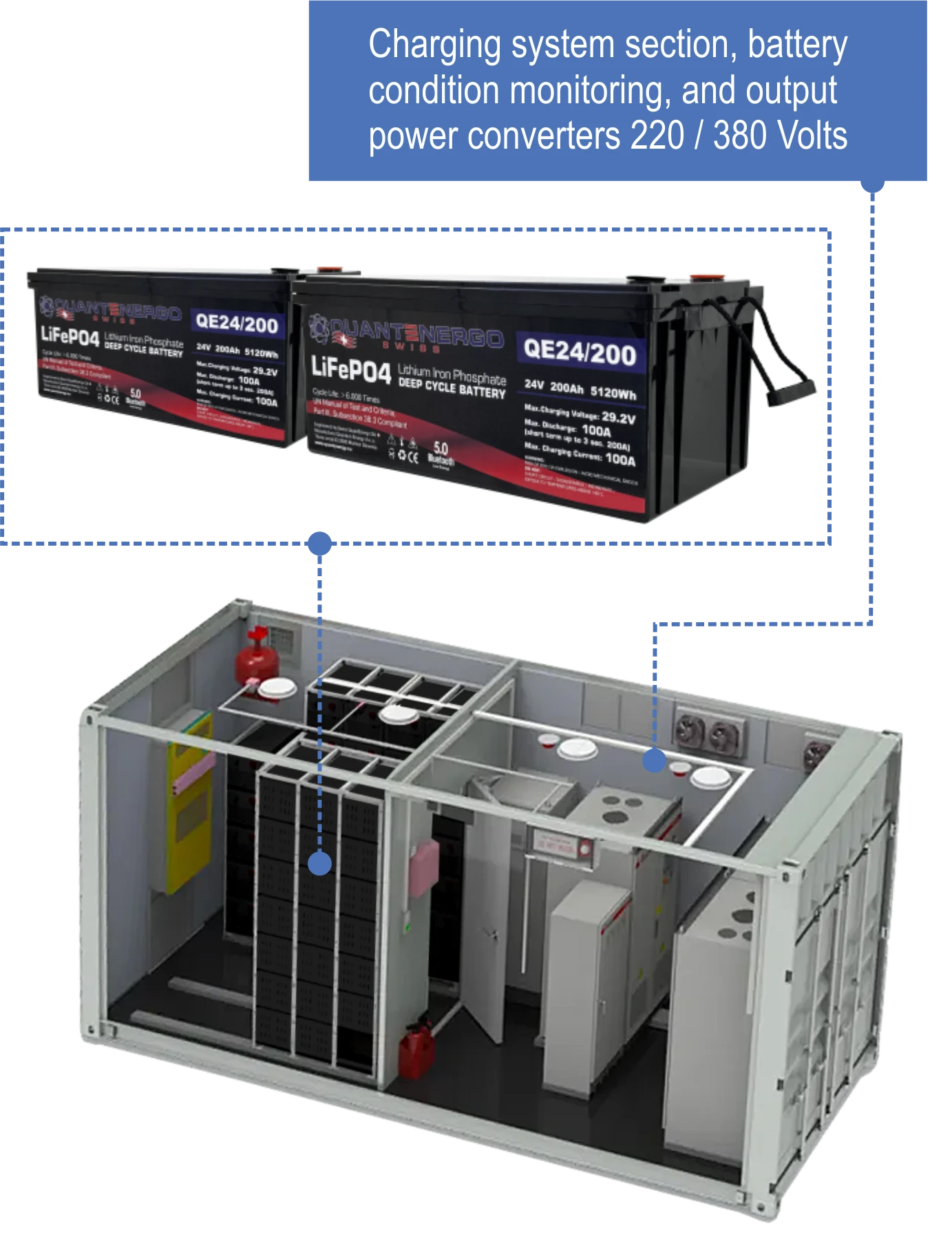
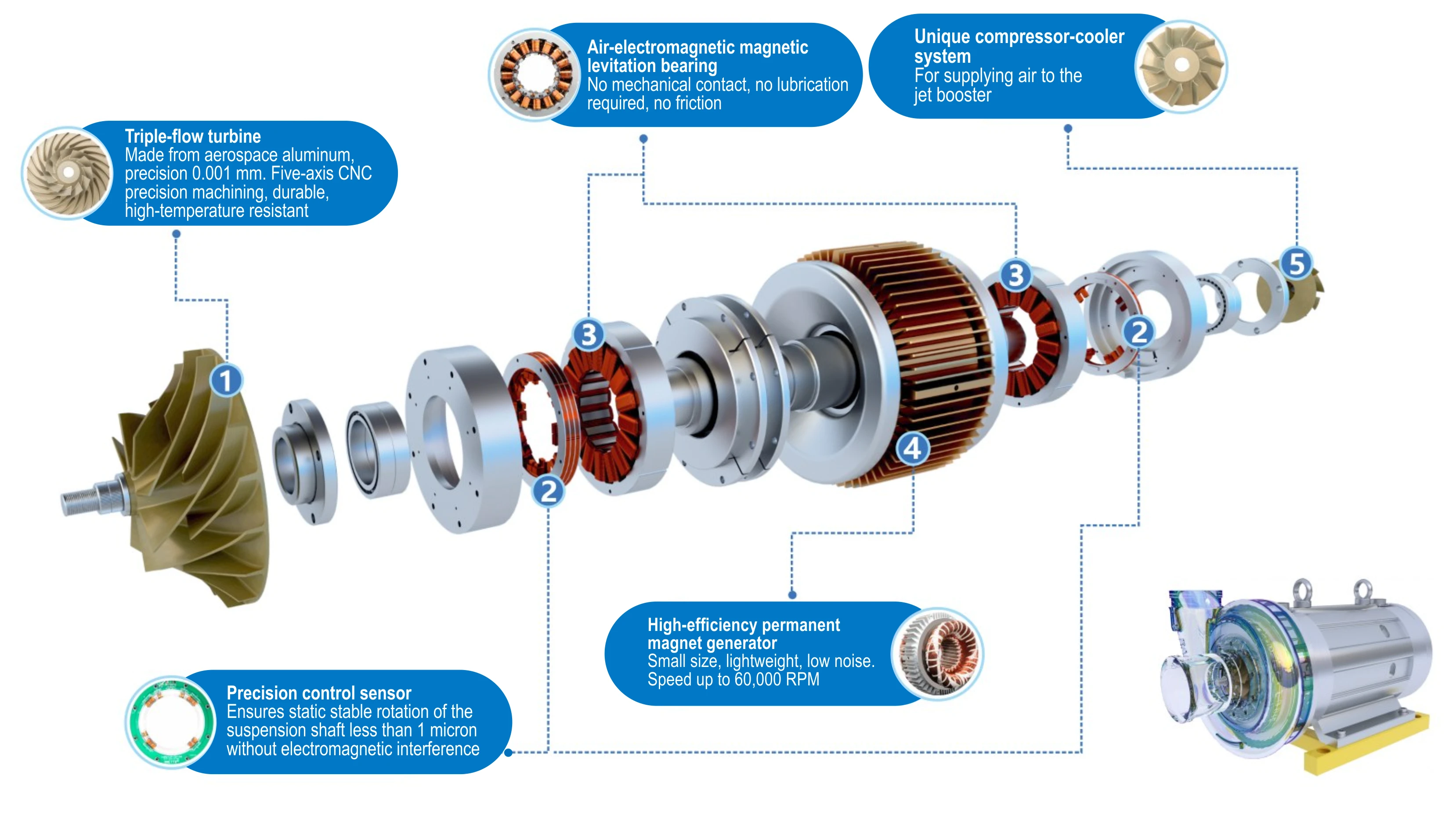
HIGH-SPEED VORTEX TURBO-GENERATOR OF THE NEW GENERATION ON MAGNETIC LEVITATING BEARINGS, POWERED BY A STEAM-HYDROGEN JET ENGINE
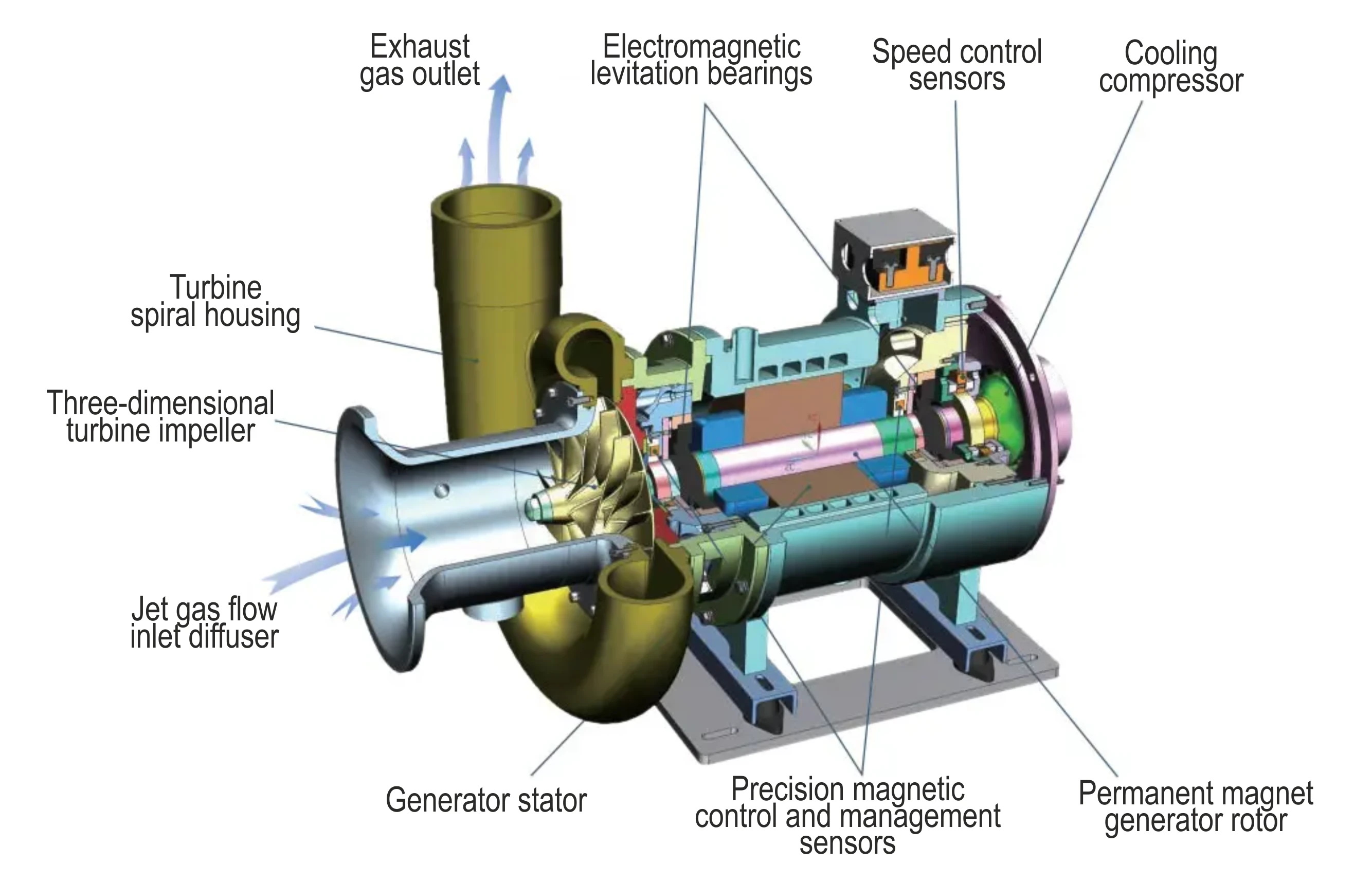
CATALYTIC REACTIVE STEAM-HYDROGEN ACCELERATOR
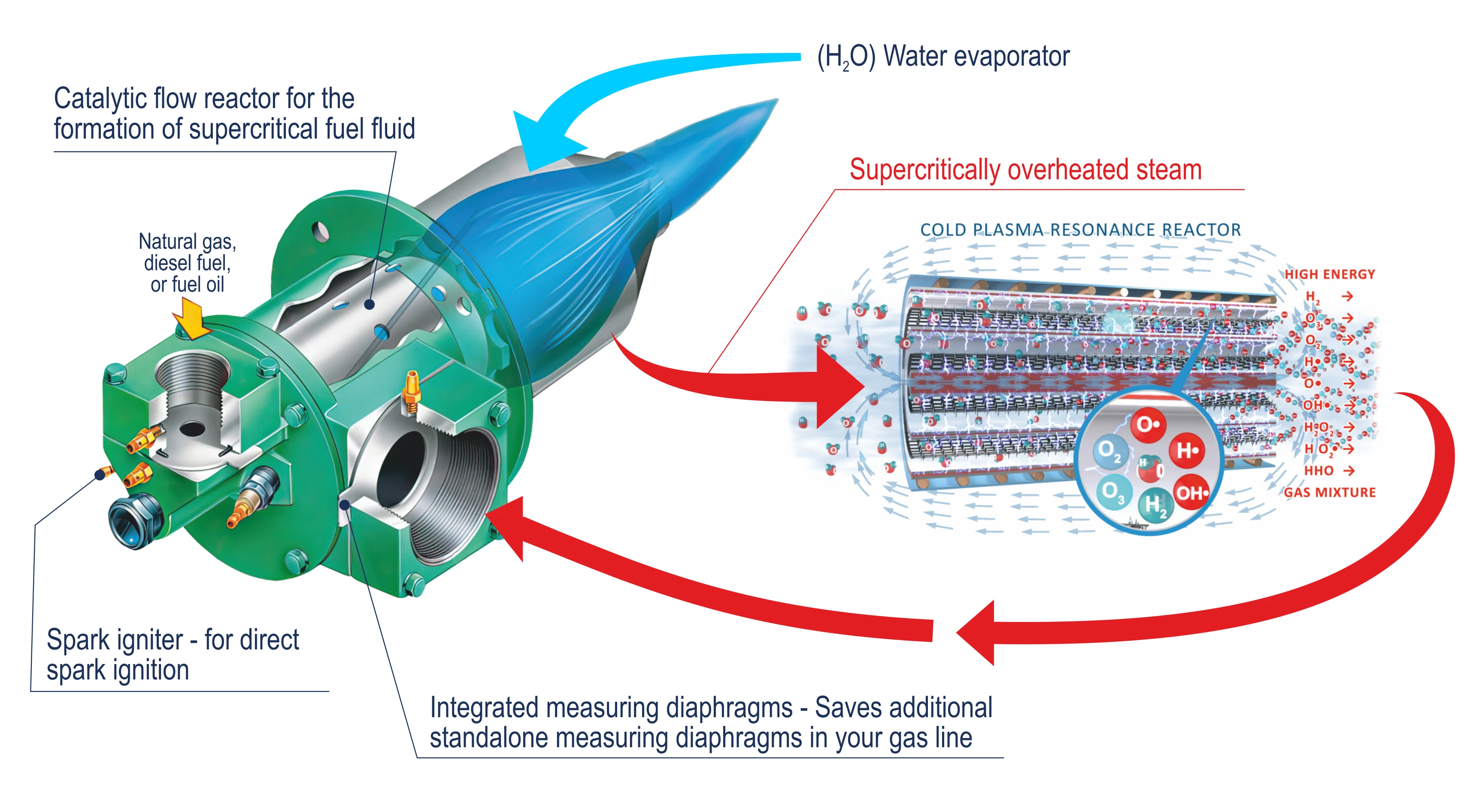
Fuel Versatility
Various types of fuel can be used, including natural gas, biogas, biomass, landfill gas, coke oven gas, blast furnace gas, coal bed methane, associated petroleum gas, diesel fuel, gasoline, kerosene, and fuel oil.
Convenient to Use
Compact, lightweight, easily movable, good expandability, remote monitoring access, and automatic operations. No rubbing mechanisms, no lubricants, no high fuel requirements.
Adjustable Operating Parameters
The heat-to-power ratio can be adjusted to adapt to varying heat conditions. Scalability is possible.
Cost-Effective
Localization of all main equipment, low maintenance costs, and a long maintenance-free operation period.
Environmentally Friendly Cycle
Low emissions of pollutants and nitrogen oxides, with noise levels controlled within 85 dB.
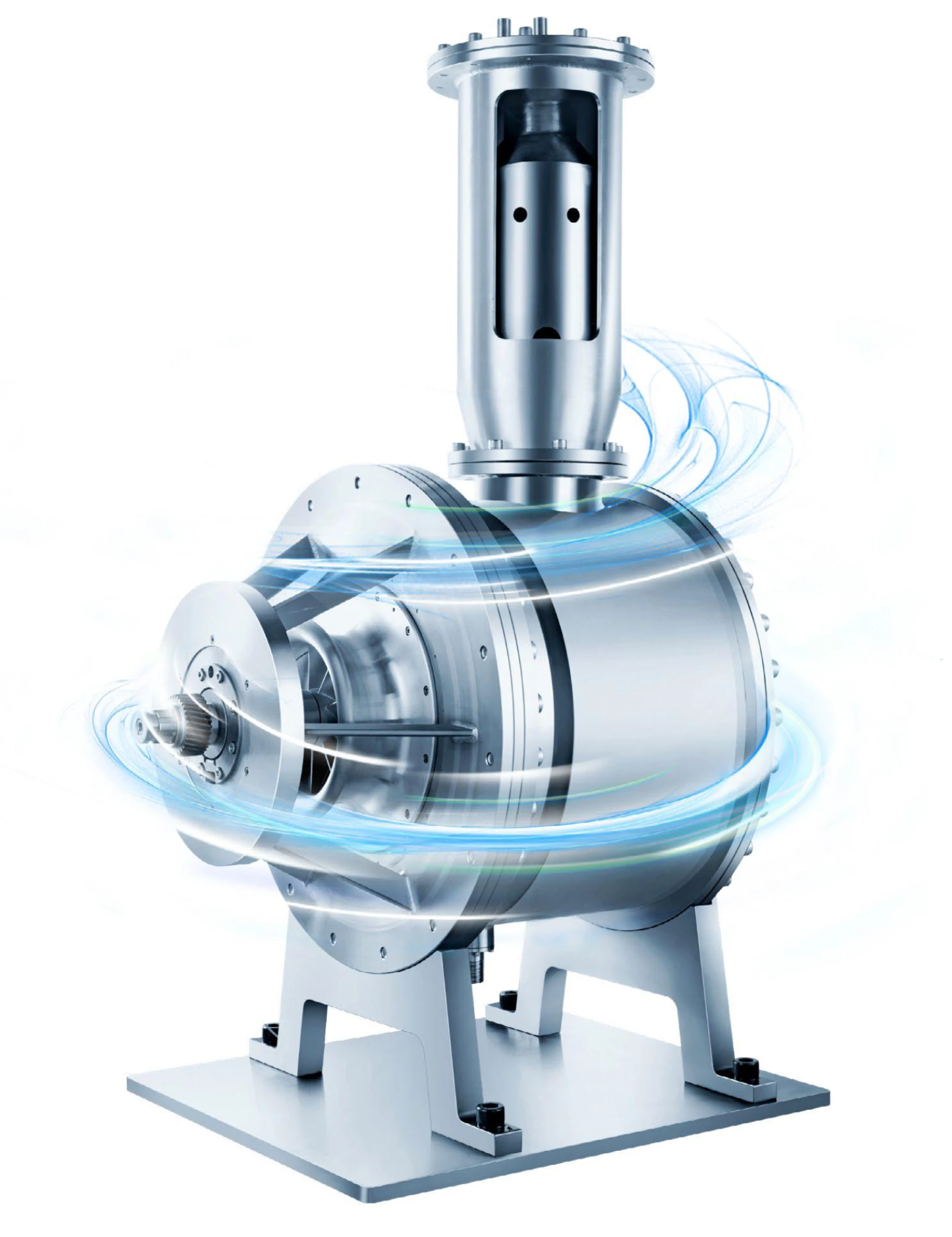
A UNIQUE INNOVATIVE DEVELOPMENT IN THE FIELD OF CATALYTIC PLASMA CHEMISTRY, ELECTROMAGNETIC TECHNOLOGIES, ULTRASONIC AND CAVITATION PROCESSES MAKES IT POSSIBLE TO CONVERT INTERNAL COMBUSTION ENGINES AND TURBOJET TURBINES TO LIQUID AND GASEOUS HIGH-ENERGY HYDROGEN-OXYGEN MIXTURES. THIS AIMS TO ACHIEVE HIGH ECONOMIC, ENERGY, AND ENVIRONMENTAL PERFORMANCE.
Instant production of high-energy, environmentally friendly hybrid liquid or gaseous fluid fuel from standard diesel, fuel oil, gasoline, and hydrogen-oxygen gas components derived from water through a plasma-chemical catalytic reaction of supercritical fluid.
This technology allows for the processing of all types of fuel, including heavy furnace oils. The technology involves the simultaneous application of multiple cavitation processes to the fuel circulating in the reactor. Under high pressure, fuel, deionized water, hydrogen, and ozone are injected through ultrasonic nozzles into an ultrasonic reactor-disperser. The resulting suspension then passes through the reactor channels, where it is subjected to a high-voltage plasma corona discharge in an intense electromagnetic field. The fuel circulation in the reactor is driven by a rotary-pulsating cavitator disperser, additionally creating a turbulent cavitation flow. During the cold plasma treatment of the suspension, fine water particles transition into a unique energetic state, forming highly reactive OH radicals, which in turn create a cascade reaction.
Molecular bonds break down, and water particles convert into hydrogen and oxygen, saturating the mixture with a high-energy component structured by the hydroxyl group OH radical.
Application areas: all diesel and gasoline engines of any design, including common rail systems. Automotive and truck transport, marine and river vessels, heating and turbojet power generation systems.
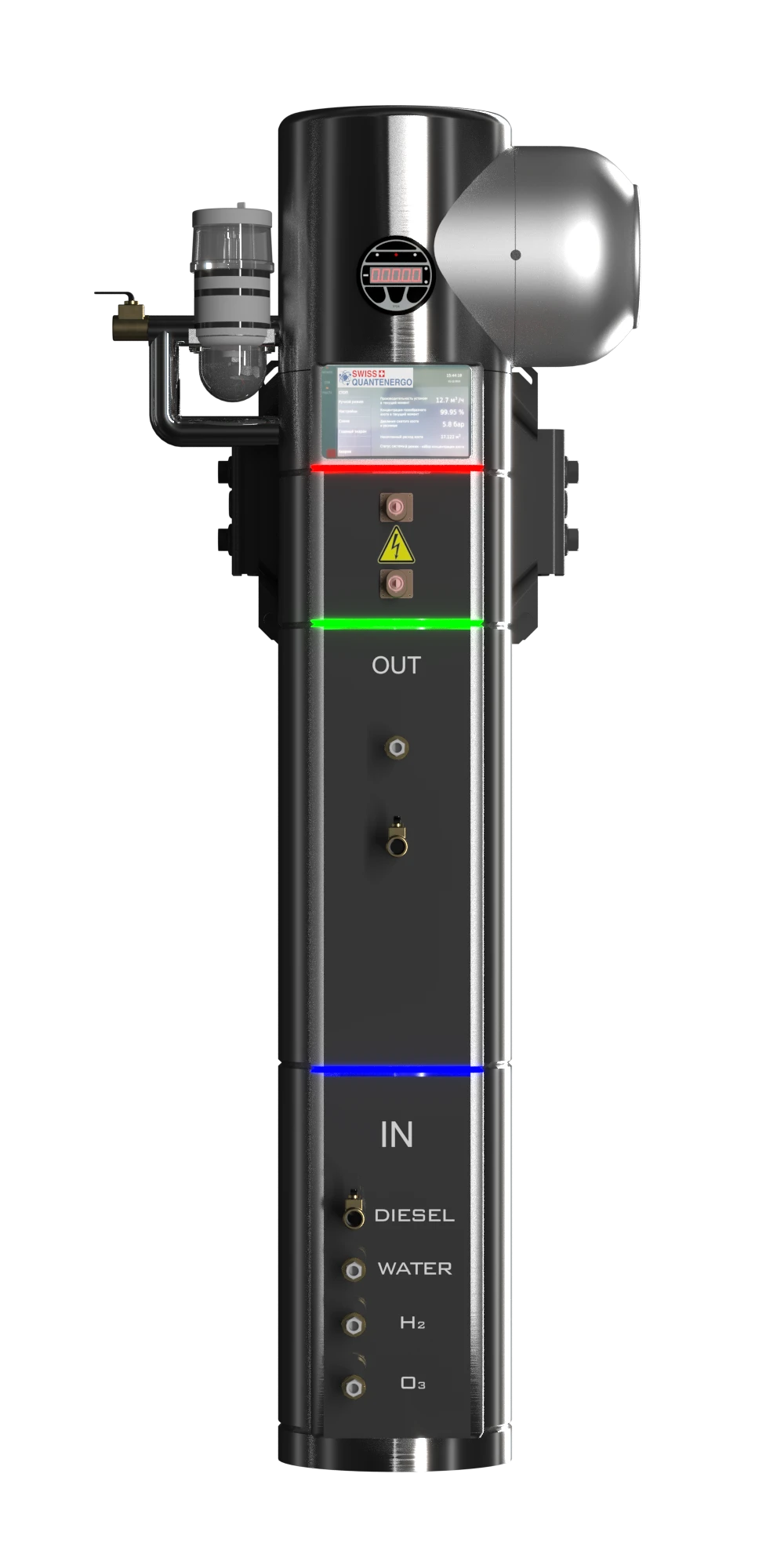
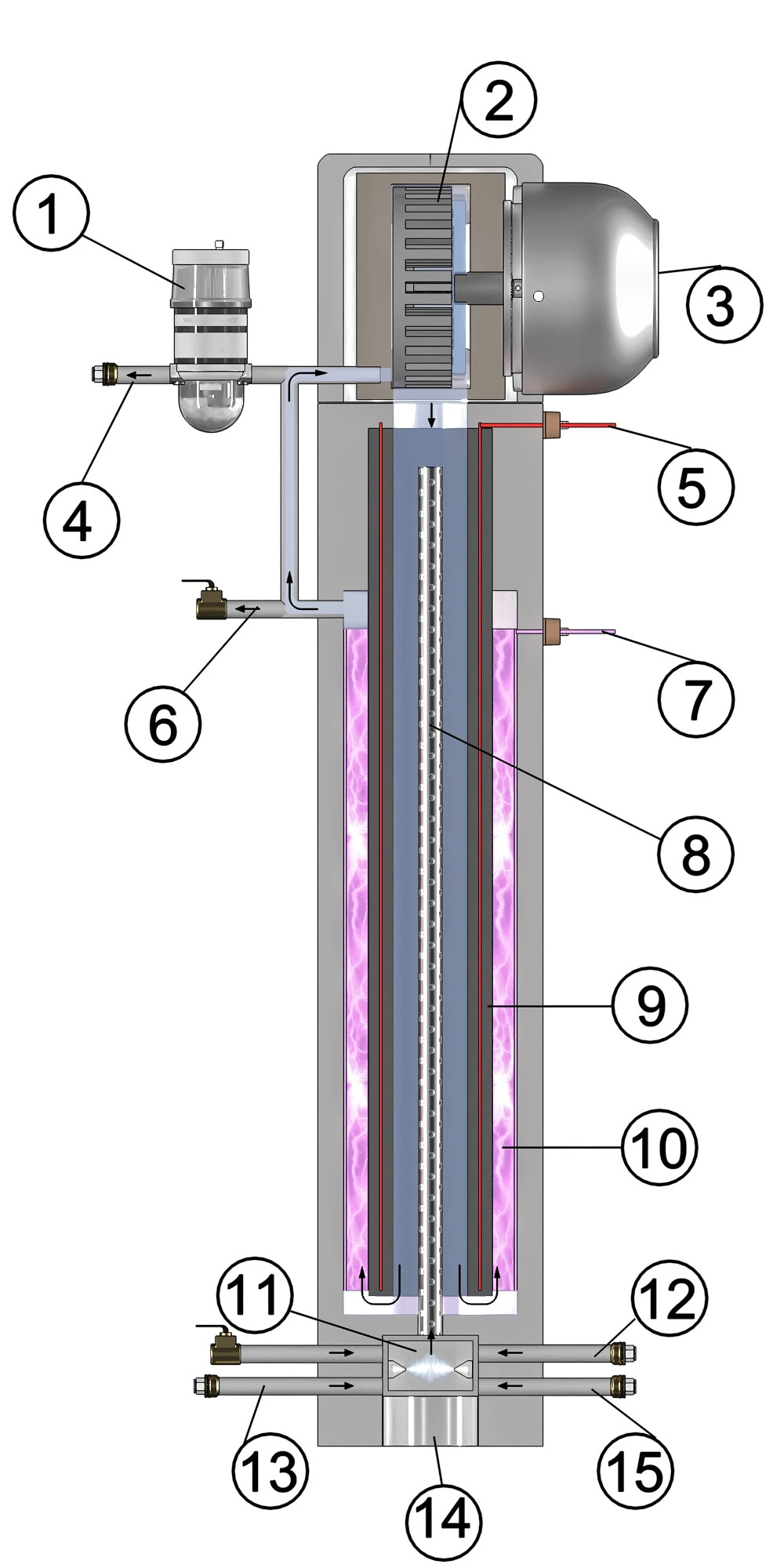
1. Gas Sampling Device
2. Rotor for Pulsation Compressor-Cavitator
3. Electric Motor
4. Outlet Channel for Undissolved Gas
5. High-Voltage Connector
6. Outlet for Prepared Emulsion on the Engine
7. High-Voltage Connector
8. Ultrasonic Resonator Emitter
9. High-Voltage Electrode
10. Cold Plasma Discharge Zone
11. Ultrasonic Mixing Chamber
12. Diesel Fuel Supply Tube
13. Hydrogen and Oxygen Supply Tube
14. Ultrasonic Radiation Generator
15. Water Supply Tube
SMALL-SIZED MULTI-FUEL POWER PLANT WITH A STEAM-HYDROGEN CATALYTIC JET ACCELERATOR
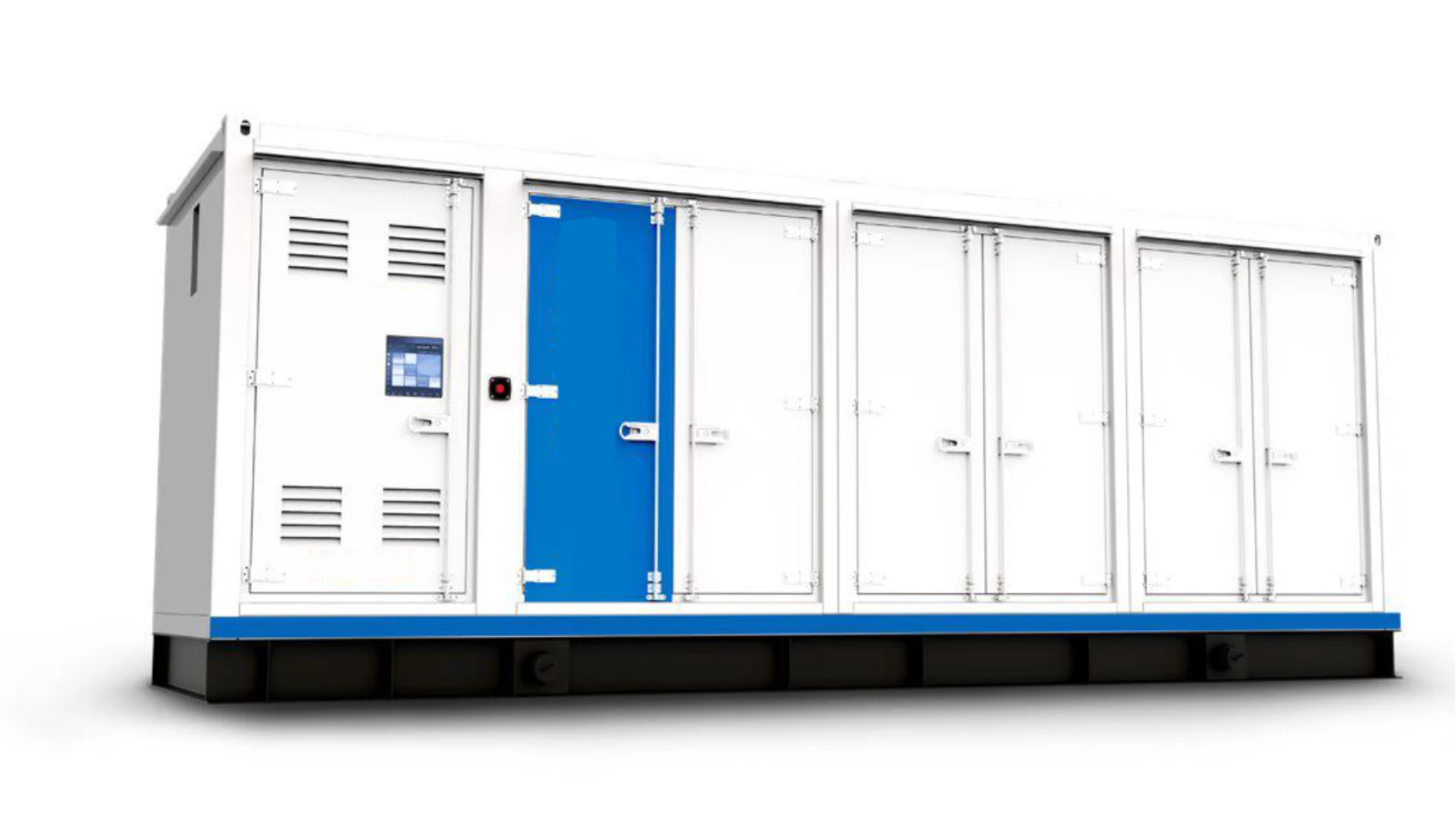
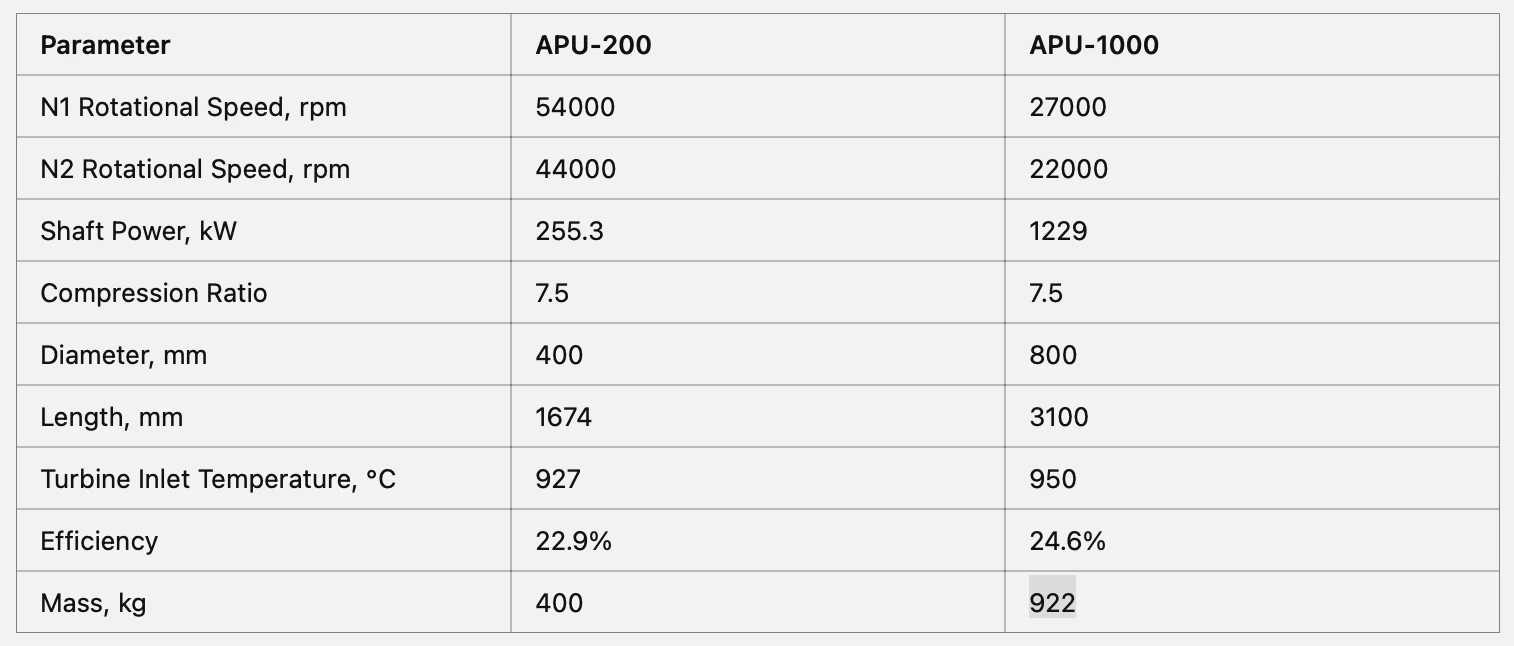
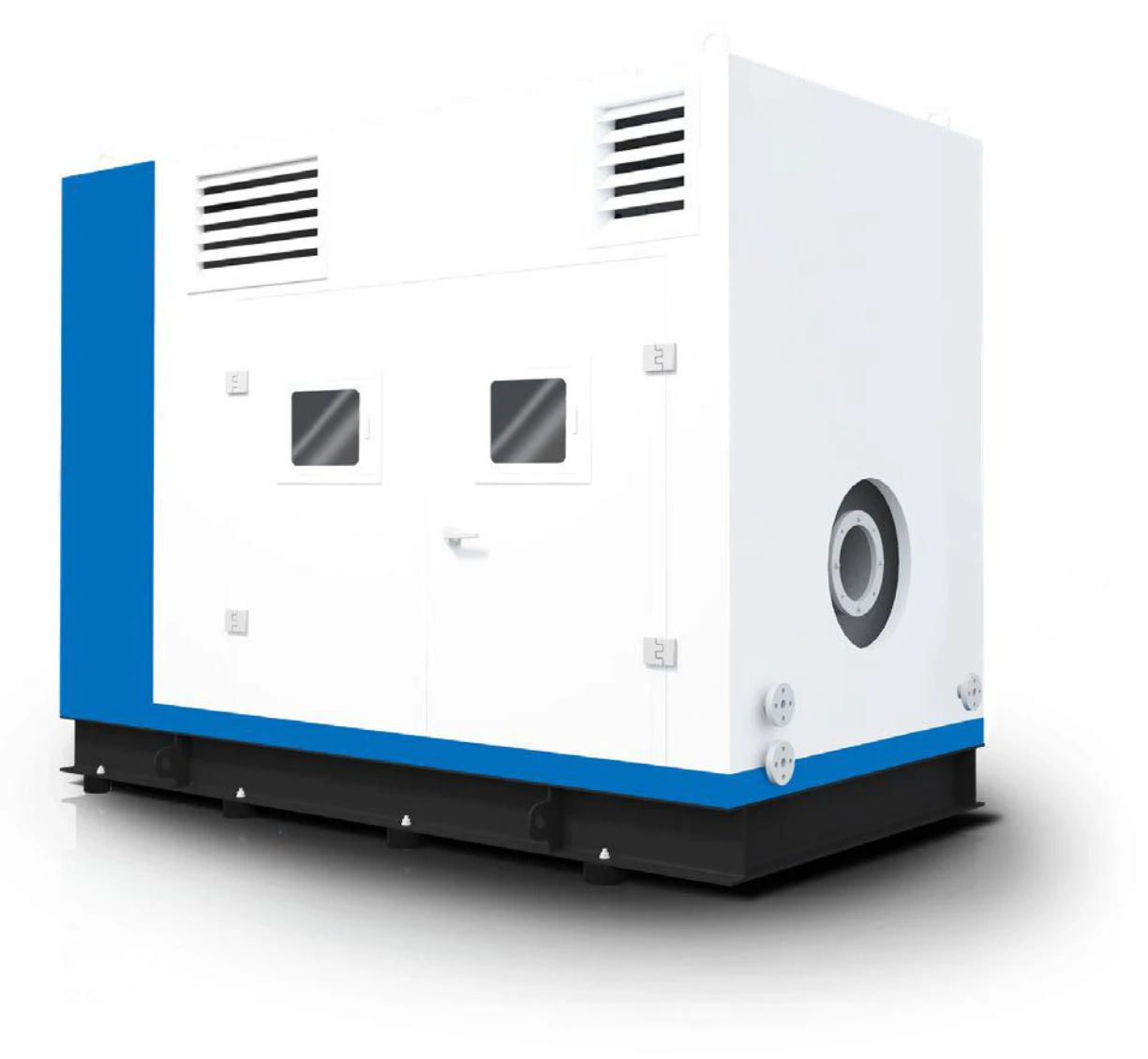
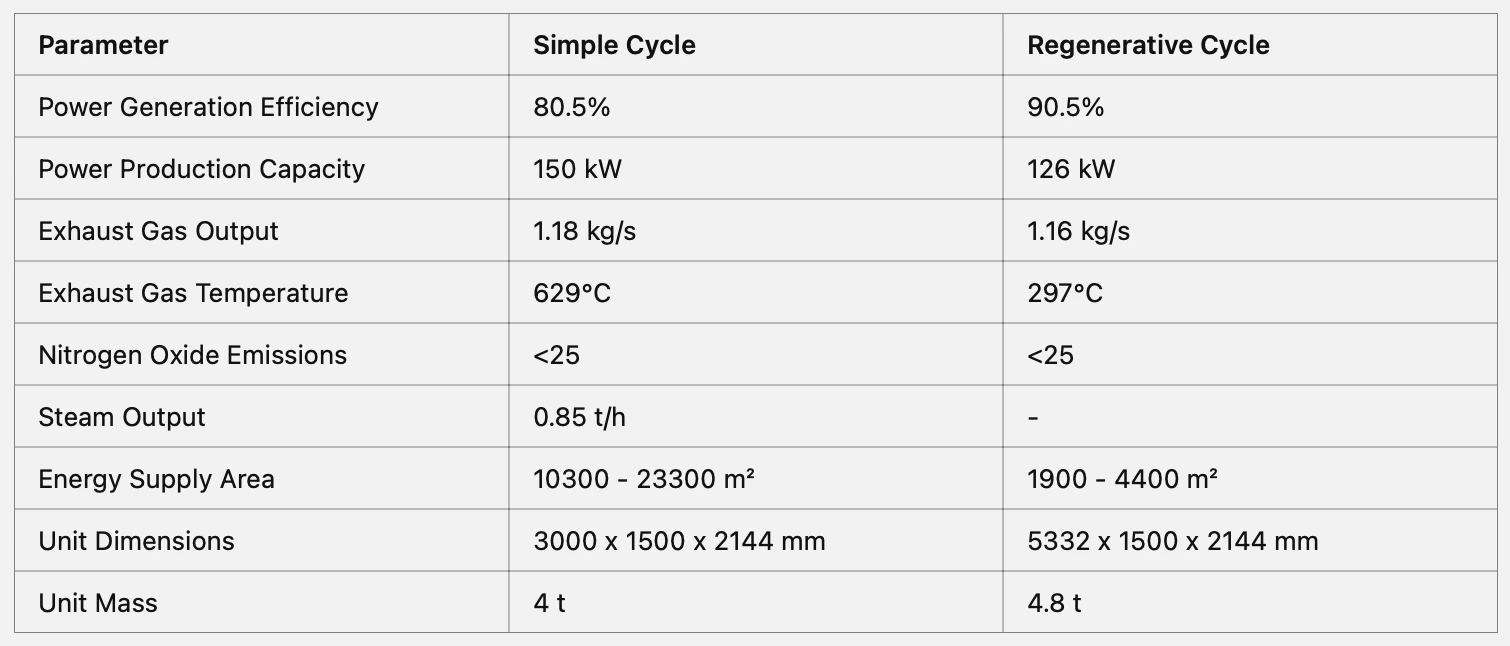
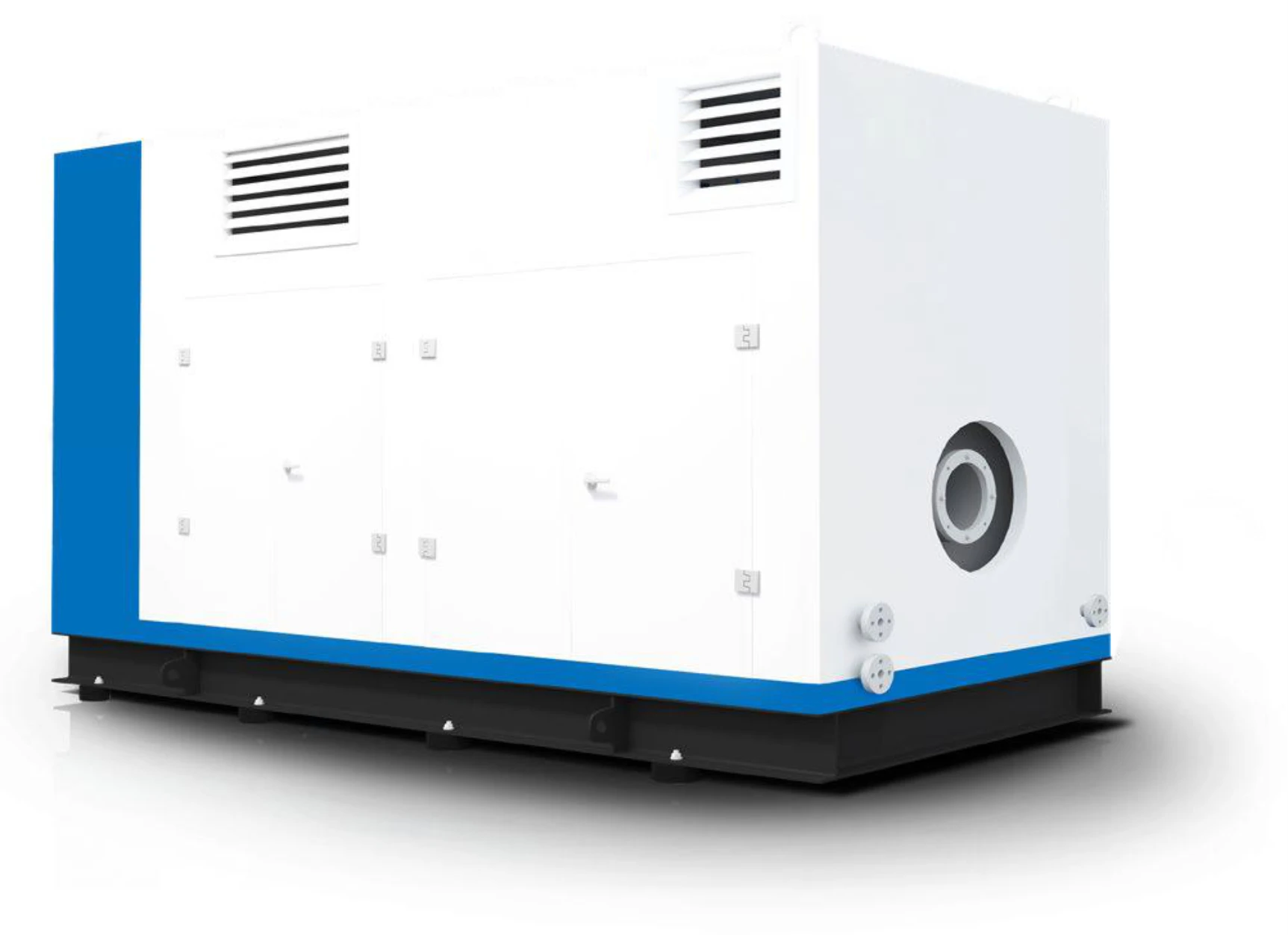
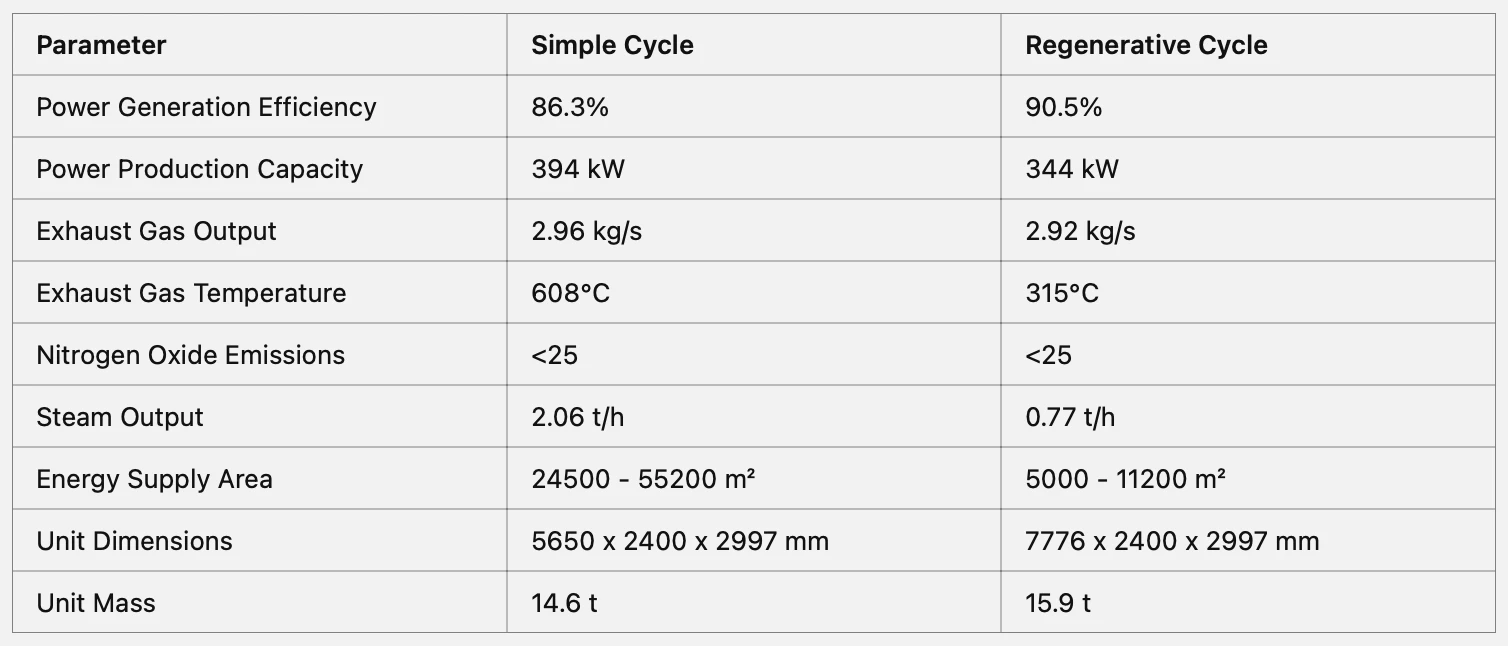
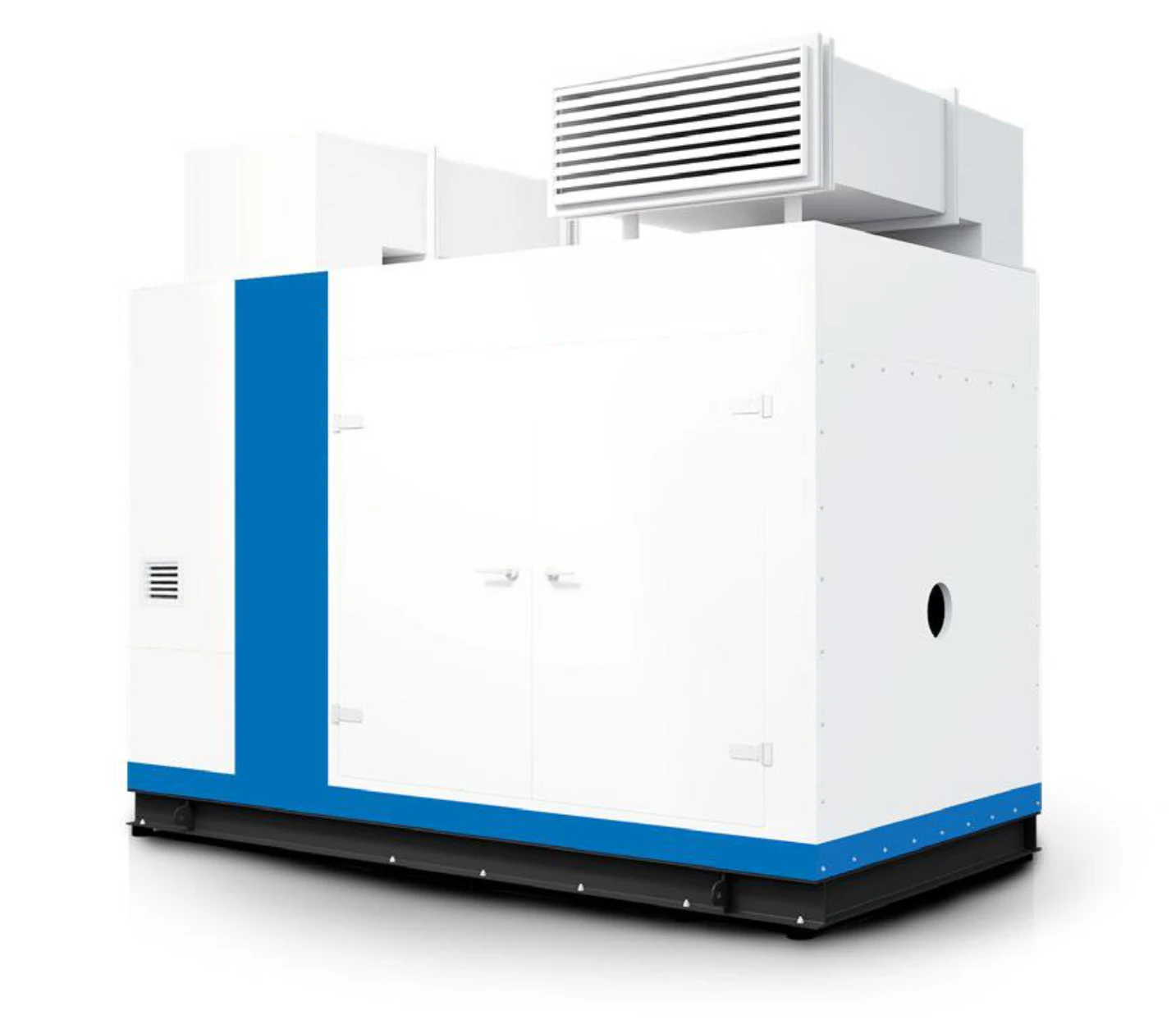
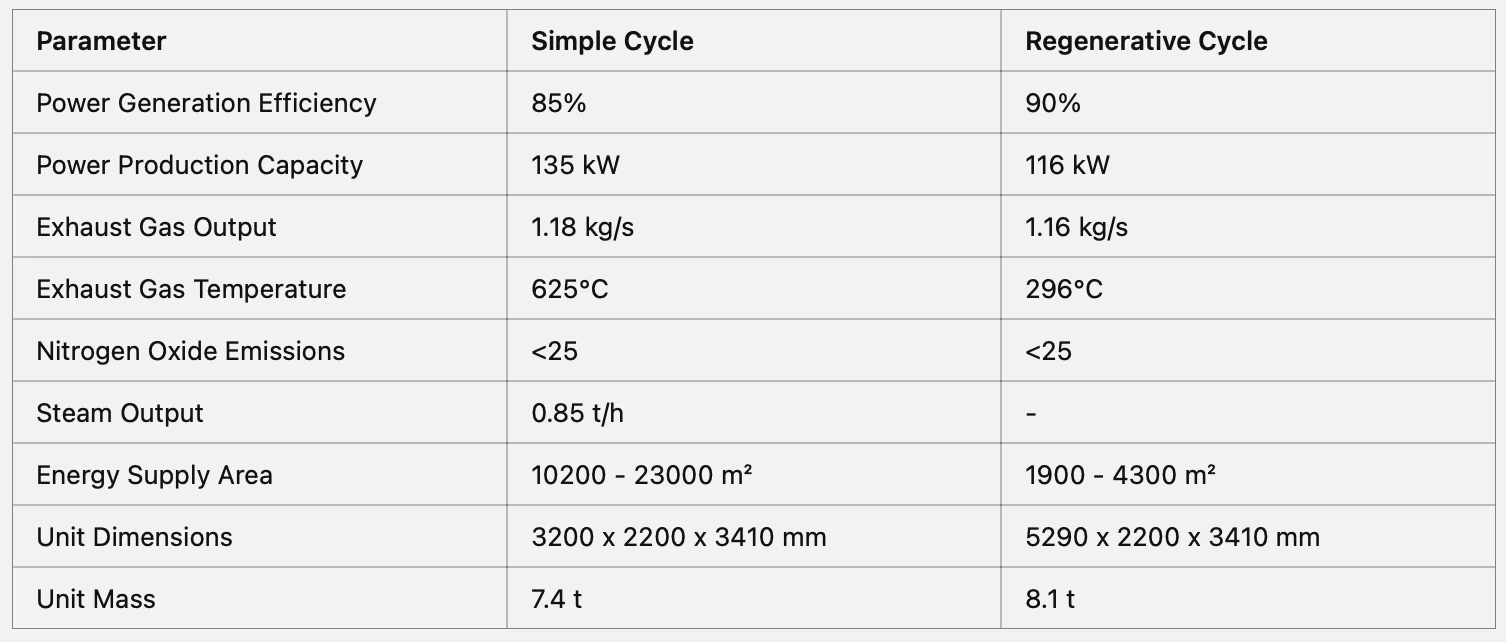